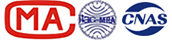
ICS83.060
G40
侣
中华人民共和国国家标准
GB/T1690-2010
代替GB/T16902006
硫化橡胶或热塑性橡胶
耐液体试验方法
Rubber, vulcanized or thermoplastic-
Determination of the effect of liquids
(ISO 1817: 2005, Rubber, vulcanized-
Determination of the effect of liquids, MOD)
量质量检
2011-01-14发布
资料专用章
2011-12-01实施
中华人民共和国国家质量监督检验检疫总局
中国国家标准化管理委员会
发布
数码防伪
GB/T1690-2010
前言
本标准按照GB/T1.1—-2009给出的规则起草。
本标准代替GB/T16902006《硫化橡胶或热塑性橡胶耐液体试验方法》,与GB/T1690—2006相
比,主要技术差异如下:
增加了一种“测量体积变化与质量变化”的试样类型,Ⅱ型:25mm×25mm的正方形(见5.2);
将式(1)△m10=m-m0×100更正为△m10=m-m×100%(见7.2);
no
一增加了一个公式(见7.3);
增加了附录B“参考液体”,以规定国产1号、2号、3号标准油的主要性能。
本标准使用重新起草法修改釆用ISO1817:2005《硫化橡胶耐液体测定方法》(英文版)。
本标准与ISO1817:2005技术性差异及其原因如下:
标准名称改为《硫化橡胶或热塑性橡胶耐液体试验方法》,因为在标准范围中已包含热塑性
橡胶
—关于规范性引用文件,本标准做了具有技术性差异的调整,以适应我国的技术条件,调整的情
况集中反映在第2章“规范性引用文件”中,具体调整如下
·用修改釆用国际标准的GB/T262代替了ISO2977(见表A.3和表B.1);
用等同采用国际标准的GB/T528代替了ISO37(见5.2和7.7);
用修改采用国际标准的GB/T1884代替了ISO3675(见表A.3;表B.2);
用等同采用国际标准的GB/T2941—2006代替了ISO23529:2004(见3.4、5.1、5.3、5.4和6.1);
用修改采用国际标准的GB/T3535代替了ISO3016:1994(见表A.4);
用修改采用国际标准的GB/T3536代替了ISO2592:2000(表A.3);
·用等同采用国际标准的GB/T6031代替了ISO48:1994(见7.6);
·用修改采用国际标准的GB/T11547代替了ISO175:1999(见A.4)。
第2章“规范性引用文件”中增加了三个文件:GB/T265,GB/T267,GB/T388。其原因是本
标准增加的附录B中提及这三个文件
测试质量变化、体积变化试样尺寸规定不同。本标准规定试样尺寸为Ⅰ型:25mm×50mm的
长方形;Ⅱ型:25mm×25mm的正方形(本版5.2)。而ISO1817:2005规定试样为1cm3
3cm3(ISO1817版5.2)。这是由于ISO标准规定范围过宽,不利于统一标准和进行数据
比对
在选择试验液体时,除了按IS01817:2005规定的 ASTM NO.1、IRM902、IRM903标准油(本
版附录A)外,还重新增加了GB/T16901992中的国产1号、2号、3号标准油(本版
附录B)。由于所采用的ISO1817:2005中规定的 ASTM NO.1、IRM902、IRM903三种标准
油还未实现国产化,需要进口,购买渠道较窄,特别是试验结果与国产1号、2号、3号标准油的
试验结果有所差异,因此,重新增加了GB/T1690-1992中的国产1号、2号、3号标准油(本
版附录B)
删除附录A.1中对制定标准模拟液体的原因说明(本版附录A,ISO1817附录A中第一段);
因为表A.1中规定已很明确。
增加了附录B“参考液体”,以规定国产1号、2号、3号标准油的主要性能。
本标准由中国石油和化学工业联合会提出
GB/T1690—2010
本标准由全国橡标委通用试验方法分技术委员会(SAC/TC35/SC2)归口。
本标准主要起草单位:中橡集团沈阳橡胶研究设计院、北京橡胶工业研究设计院、西北橡胶塑料研
究设计院。
本标准主要起草人:费康红、赵博丹、谢君芳、朱伟。
本标准所代替标准的历次版本发布情况为:
GB/T1690-1987、GB/T1690-1992、GB/T1690-2006。
GB/T1690-2010
引言
液体对硫化橡胶或热塑性橡胶的作用通常导致以下结果:
a)液体被橡胶吸入;
b)抽出橡胶中的可溶成分;
c)与橡胶发生化学反应。
通常,吸人量a)大于抽出量b),导致橡胶体积增大,这种现象被称为“溶胀”。吸入液体使橡胶的拉
伸强度、拉断伸长率、硬度等物理及化学性能发生很大变化。此外,由于橡胶中增塑剂和防老剂类可溶
物质,在易挥发性液体中易被抽出,其干燥后的物理及化学性能同样会发生很大变化。因此,测定橡胶
在浸泡后或进一步干燥后的性能很重要。
本标准规定了确定下列性能变化的测试方法
质量变化、体积变化、尺寸变化;
抽出物;
浸泡后或进一步干燥后橡胶的硬度变化、拉伸性能变化。
本标准所提供的测试方法在某种程度上模拟了一些实际使用条件,但并不意味着可完全代表实际
使用性能。例如,试验显示体积变化最小的橡胶材料并不一定代表实际使用性能最好。对于非常厚的
橡胶制品,厚度的变化对耐液体性能影响不大,但对于一般橡胶制品,由于液体渗透速度与时间关系很
大,因此测试时必须考虑到橡胶的厚度。另外,大气中氧气的存在会影响液体对橡胶的作用,特别是在
高温条件下。本标准描述的试验方法可对橡胶与给定液体使用的相宜性提供有价值的信息,特别是为
橡胶耐液体性能的开发与研究构建了一个有效的控制。
液体对橡胶的影响取决于橡胶特性和橡胶内部应力的大小。在本标准中,所有试验均在试样无外
力作用下完成。
GB/T1690-2010
硫化橡胶或热塑性橡胶
耐液体试验方法
警告:使用本标准的人员应有正规实验室工作的实践经验。本标准并未指出所有可能的安全问题,
使用者有责任采取适当的安全和健康措施,并保证符合国家的有关法律法规的规定。
1范围
本标准规定了通过测试橡胶在试验液体中浸泡前、后性能的变化,评价液体对橡胶的作用。试验液
体包括标准试验液体及类似于石油的衍生物、有机溶剂、化学试剂等
本标准适用于硫化橡胶或热塑性橡胶
2规范性引用文件
下列文件对于本文件的应用是必不可少的。凡是注日期的引用文件,仅注日期的版本适用于本文
件。凡是不注日期的引用文件,其最新版本(包括所有的修改单)适用于本文件。
GB/T262石油产品和烃类溶剂苯胺点和混合苯胺点测定法(GB/T262-2010,ISO2977:1997,
MOD)
GB/T265石油产品运动粘度测定法和动力粘度计算法
GB/T267石油产品闪点与燃点测定法(开口杯法)
GB/T388石油产品硫含量测定法(氧弹法)
GB/T528硫化橡胶或热塑性橡胶拉伸应力应变性能的测定(GB/T528-2009,ISO37:2005
IDT)
GB/T1884原油和液体石油产品密度实验室测定法(密度计法)(GB/T18842000,
eqv iso3675:1998)
GB/T2941橡胶物理试验方法试样制备和调节通用程序(GB/T2941-2006,ISO23529:2004,
IDT)
GB/T3535石油产品倾点测定法(GB/T3535—2006,ISO3016:1994,MOD)
GB/T3536石油产品闪点和燃点的测定克利夫兰开口杯法(GB/T35362008,ISO2592:
2000,MOD
GB/T6031硫化橡胶或热塑性橡胶硬度的测定(10~100IRHD)(GB/T6031--1998, idt Iso48:
1994)
GB/T11547塑料耐液体化学试剂性能的测定(GB/T11547-2008,ISO175:1999,MOD)
ISO3104石油产品透明和不透明液体运动黏度的测定和动力黏度的计算( Petroleum
products- Transparent and opaque liquids Determination of kinematic viscosity and calculation of
dynamic viscosity
ISO561石油产品液态烃类折光指数的测定( Petroleum products-Hydrocarbon liquids
Determination of refractive index)
标准分享网ww.bzfxw.com免费下载
GB/T1690-2010
3试验装置
3.1全浸装置
设计时应考虑液体的挥发性和试验温度,以使试验过程中液体的挥发程度最小及外部进入试验容
器的空气最少。
当试验温度明显低于试验液体的沸点时,试验容器应使用带盖的玻璃容器。如果试验温度接近液
体的沸点,建议使用带有回流冷凝器的容器或通过共他方式以减少液体挥发。
试验容器的尺寸应保证试样在不发生任何变形的情况下完全浸入液体。试验液体的体积至少为试
样总体积的15倍,试验容器中液体上部空气体积癍尽可能达到最小
用线或棒将试样吊入液体电确保试样与试样之间不接触可用玻璃环或其他不发生反应的间
隔物。
试验容器所用的材料不试验液体及试样发生反应,如:不应使用含铜类材料
3.2单面试验装置
此装置用于试样仅有一个表面与液体接触的试验。
试验装置如图所示:包括一个底板(A)和一个底部开口的圆柱形容器(B,通过蝶型螺母(D)与
螺栓(E)将A、B与试样(C紧紧固定在一起。底板可留一个直径约30mm的孔以确认试样另一面未
与试验液体相接触》在试验期间,容器上部的开口处应用一合适的盖子(F密封
单位为毫米
D
E
B
N
530
450±1
图1单面试验装置
3.3天平
天平应精确到1mg
GB/T1690-2010
3.4试样测厚装置
将一个满足精度要求的百分表固定在一个带有平台的钢架上。该装置应符合GB/T2941中方法
A的要求
3.5测量试样长度和宽度的装置
最小分度为0.01mm,宜采用非接触法测量,例如使用光学测量仪器
3.6测量表面积变化的装置
能够测量试样对角线的长度。
与测量试样长度和宽度装置的要求相同。
4试验液体
试验液体的选择应依据试验目的。
如需得到一种硫化橡胶与一种特定液体的实际使用性能,则试验应尽量使用该种液体。市售液体
的组分不一定总是恒定的,每次试验应包括一个已知性能的标准材料。如果发生由于市售液体组分变
化而产生异常结果的情况,则不应再使用该批液体。
矿物油和燃油。生产批次不同化学组成也很容易发生变化。通常,矿物油的苯胺点高低可用于指
示芳香烃的含量,并且有助于显示该油对于橡胶的作用,但是仅凭苯胺点一项指标,不能完全显示一种
矿物油的特性,苯胺点越低对橡胶的溶胀作用越强。如果使用矿物油作为试验液体,若有必要,则试验
报告应包括液体的密度、折光指数、黏度及苯胺点或芳香烃含量。附录A和附录B提供的标准试验油,
由矿物残液提炼、加工而成。
试验用油。尽管有些试验用油与标准油(附录A,A.1~A.3及附录B)的液体特性相似,但对橡胶
的作用却不完全相同。一些燃油,特别是汽油,组成成分相差很大,对于某些成分,较小的改变,可对橡
胶的作用产生很大影响。因此,使用燃油做耐液体试验时,若有必要,试验报告中应包括完整液体组成
成分的描述。
商品液体的组成成分也不总是恒定的,标准液体有明确的化学成分和化学混合物成分,用于进行硫
化橡胶分类或质量控制试验,附录A给出了一些适合的液体。当试验液体为化学试剂时,试剂的浓度
应适于使用目的。应确保试验液体在整个试验过程中组成成分不发生过大变化。应考虑试验液体的自
身老化现象及其可能与橡胶发生的任何反应。如果液体中有活性添加剂,或者橡胶与液体通过抽出、吸
入或发生化学反应而使液体组成变化较大,应考虑补充液体的体积或定期更换新的试验液体。
5试样
5.1试样制备
试样制备按GB/T2941的规定。
5.2试样尺寸
试样厚度为2.0mm±0.2mm。试样也可从制品上裁切,若厚度小于1.8mm,则以该试样的实际
厚度作为试验厚度。如果试样厚度大于2.2mm,应将厚度处理到2.0mm±0.2mm。不同厚度的试
样测试结果不具有可比性。
GB/T1690-2010
测量体积变化与质量变化试样为型:25mm×50mm的长方形;型:25mm×25mm的正方形
注:两种规格的试样,测得结果不可进行比较。建议优先选用Ⅰ型试样
测量硬度变化的试样横向尺寸不小于8mm。
测量尺寸变化所用试样可选Ⅰ型或Ⅱ型试样,还可以选直径为44.6mm的圆形试样(GB/T528中
A型标准环状试样的内圆)。
测表面积变化的试样为垂直裁切的平行四边形,可通过两次连续的、方向近似垂直的裁切完成。裁
刀由两个相隔规定距离的刀片组成。试样边长约为8mm。
注:测试样表面积变化也可以使用更小或更溥的试样,例如从产品上裁切或快速检测试验等。但这样的测试结果
与规定厚度试样的测试结果不可比较。更小的试样会降低测量结果的精确性。
测试拉伸性能变化的试样按GB/T528的规定,宜选择2型哑铃状试样。该形状试样也可用来测
试硬度变化
单面接触试验所用的试样为直径约60mm的圆形试片。
5.3硫化与试验时间间隔
如无特殊规定,硫化与试验时间间隔应按以下GB/T2941的规定。
对所有试验,硫化与试验之间最短时间间隔为16h
对于非制品试验,硫化与试验之间最长时间间隔为4周。做比对及评价试验,应尽可能在相同的时
间间隔内进行
对于制品试验,硫化与试验之间时间间隔不应超过3个月。在其他情况下,试验应在接到客户提供
试样2个月内完成
5.4试样调节
试样应在GB/T2941规定的标准实验室温度下调节至少3h。进行比对试验时,应始终保持同
温度。
6试验液体浸泡的温度及周期
6.1温度
浸泡温度应选用GB/T2941中8.2.2所列出的一个或多个温度。
高温试验可加速橡胶的氧化和液体的挥发与分解,同时,促进液体中添加剂对橡胶的影响。浸泡温
度的选择应按GB/T2941提供的、与实际使用温度相同或高于实际使用温度的试验温度。
6.2周期
由于液体渗透橡胶的速度取决于温度、胶种、液体种类,因此,所有试验均使用同一标准时间是不可
取的。尽可能做重复多次浸泡试验,并记录浸泡性能随时间的变化情况,以确定合适的试验时间。试验
时间宜大于液体吸收饱和的时间。
作为质量控制试验,用一种浸泡周期已可以满足要求,但应尽可能大于吸收饱和时间。试验时间应
从以下时间范围内选择:
24-2h;72-2h;7d±2h;7d土2h的整数倍。
注1:由于吸收液体的量与时间的平方根成比例而不是时间本身,这样可通过绘制吸收量与时间平方根的曲线来确
定液体吸收饱和的时间
注2:在浸泡试验初期,性能变化百分数与试样厚度的倒数成正比。因此,当试验时间未达到吸收饱和时间时,试样
厚度的差异越小得到的试验结果越稳定。
GB/T1690-2010
7程序
7.1通用试验程序
每组测试需用3个试样,在浸泡前做好标识。
将试样浸入盛有试验液体(4)的装置(3.1或3.2)中,并将装置放入已达到所需温度(6.1)的恒温箱
或液体加热恒温装置中。
对于全浸试验,试样应距离容器内壁不少于5mm,距容器底部和液体表面不少于10mm。如果
橡胶密度小于液体密度,应加坠子将试样完全浸没在液体中。同时,应避免空气的进入,如需测试空气
对试验的影响,则相关方应协商确定允许空气进入的程度。
在浸泡试验结束后,从恒温箱或液体加热恒温装置中取出试验装置,在标准实验室温度下调节
30min。或将试样取出快速放入一份已备好的新试验液体中,在标准试验温度下停放30min
除去试样表面的残留液体。若试验液体为易挥发性液体,用滤纸或不掉绒的织物迅速擦去试样表
面残留液体。若为黏性不挥发性液体,可用滤纸擦去。如有必要,也可迅速将试样浸入酒精或汽油等挥
发性液体中,然后迅速取出并擦干试样表面。再进行性能测试。
对于挥发性液体,将试样取出之后的每一步操作应尽快完成。在擦去表面残液后,迅速将试样放入
称量瓶中测量橡胶的体积变化与质量变化。测完后,如果还需用此试样测量其他性能,则应将试样重新
浸入此挥发性液体中,浸泡周期应满足6.2的规定。将试样从液体中取出至性能全部测试完毕,不应超
过以下时间:
尺寸变化:1min;
硬度变化:1min;
一拉伸试验:2min
如试验还需继续进行,则应将试样再次快速浸入液体中,并将测试装置放回恒温箱或液体控温装
置中。
也可测量干燥后的性能变化。取出浸泡的试样放入一个绝对大气压约20kPa,温度约40℃的一
定容积的设备中,每间隔30min取出试样称量一次,直至两次称量之差小于1mg为止。然后在标准实
验室温度下环境调节不少于3h,再进行试验
7.2质量变化
在标准实验室温度下测量试样浸泡前后的质量,精确到1mg。
按式(1)计算质量变化百分率(△m100):
△m100
100%
……………………(1)
式中
ma—浸泡前试样在空气中的质量,单位为克(g);
m—浸泡后试样在空气中的质量,单位为克(g)。
取三个试样试验结果的中位数作为试验结果
7.3体积变化
对于非水溶性液体一般采用排水法测量。
在标准实验室温度下,先测每个试样在空气中的质量(m),精确到1mg,再测试样在蒸馏水中的质
量(ma,),精确到1mg,在蒸馏水中测量质量时应排除试样上的气泡(必要时可用洗涤剂)。按式(2)
计算
5
标准分享网ww.bzfxw.com免费下载
GB/T1690-2010
)×100%
式中:
7
浸泡前试样在空气中的质量,单位为克(g);
浸泡后试样在空气中的质量,单位为克(g);
m,—浸泡前试样在蒸馏水中的质量,单位为克(g);
ni, w
浸泡后试样在蒸馏水中的质量,单位为克(g)。
取三个试样试验结果的中位数作为试验结果。
如果材料密度小于1g/cm3,需加坠子测量,测量中应确保坠子与试样全部浸入水中,还应测量单
个坠子在水中的质量(m,),用式(3)计算体积变化百分数(△V100)。
△Vn=(m-m+m-1)×100%
…(3)
式中:
浸泡前试样在空气中的质量,单位为克(g);
浸泡后试样在空气中的质量,单位为克(g);
mw—浸泡前试样在蒸馏水中的质量(带坠子),单位为克(g);
i, w
浸泡后试样在蒸馏水中的质量(带坠子),单位为克(g);
m2,w坠子在蒸馏水中的质量,单位为克(g)。
取三个试样试验结果的中位数作为试验结果。
若试验液体溶于水或与水发生反应,试验后不应用水称量。若试验液体不太黏稠或室温下不易挥
发,可在新配制的同样试验液体中称量。若试验液体不适于称量,试验后也可选用其他液体称量。按
式(4)计算:
△V1=「1/m二m+mnm)-1×100%
……………………(4)
0
式中:
液体密度,单位为克每立方厘米(g/cm3)
m,-浸泡后试样在新配制的试验液体中的质量(含坠子),单位为克(g);
m—坠子在新配制的试验液体中的质量,单位为克(g)。
7.4尺寸变化
在标准实验室温度下,沿着靠近试样的中心线处测量试样长度(宽度),精确到0.5mm,取上下表
面两次测量结果的平均值。用厚度计在试样的四个不同位置测量厚度取其平均值。
浸泡后的试样按上述规定进行。
用式(5)计算长度变化百分率(△L100):
△L
li-Lo
100%
式中:
l0试样的初始长度,单位为毫米(mm);
l1—试样浸泡后的长度,单位为毫米(mm)。
用同样的方法计算宽度变化百分率和厚度变化百分率
取三个试样试验结果的中位数作为试验结果
表面积变化百分率也可通过长度变化及宽度变化来计算。
7.5表面积变化
在标准实验室温度下测量试样初始对角线的长度,精确到0.01mm。
GB/T1690—2010
浸泡后按上述方法重新测量对角线的长度。如果采用光学仪器测量,试样也可以不从液体中取出,
直接透过合适的玻璃容器即可进行测量
用式(6)计算表面积变化百分率(△A10)
△A00=/Al
L,4-1)×100%
………(6)
式中
l2,lb—试样浸泡前两条对角线的长度,单位为毫米(mm);
2A,4a—试样浸泡后两条对角线的长度,单位为毫米(mm)。
也可用式(7)计算体积变化百分率
3/2
△V100
100%
L,lu
…………………………(7)
用式(7)计算体积变化应是假设其膨胀是同向的,如果不确定,宜采用7.3的方法计算体积变化百
分率。
7.6硬度变化
按GB/T603M法测量浸泡前后每个试样的硬度。也可以用普通硬度计三片叠加测量,但这
种方法只作常规硬度检测。
按式(8)计算试验前后的硬度变化(△H
AH=H、H
…t………………(8)
式中:0
H。—试杖泡前的硬度;
H1—试样浸泡后的硬度
7.7拉伸性能变化率
按GB/T524规定,测定试样浸泡前后的拉伸性能
用试样初始面积计第拉伸强度拉断伸长率和定伸应力
按式(9)计算划伸能变化百分率(△xm)
△X1
100%
……(9)
式中:
X。试样浸泡前的性能值
X,—试样浸泡后的性能值
7.8单面试验
本方法适用于仅有一个表面与液体接触的较薄片材(如橡胶薄膜)。
测量试样的厚度,然后称量试样在空气中的质量(m0),精确到1mg。将试样装入如图1所示的装
置中,将试验液体倒入装置内,深度约15mm,盖上盖子(F)。
将装置放入已调好的恒温试验箱中至要求的试验时间,将装置取出,如有需要,调节至实验室标准
温度。将试验液体倒出,取出试样,用滤纸或不掉绒织物擦去试样表面的残留液体。之后,在标准实验
室温度下称量试样质量(m;),精确到1mg,并测量试样厚度。
如果在室温下试验液体易挥发,则试样从液体中取出后,应在2min内完成测试。
按式(10)计算单位面积的质量变化率(△mn),单位为克每平方米(g/m2)。
△m=m;-m10
A
………………(10)
GB
3/T
1690-2010
式中:
m试样的初始质量,单位为克(g);
m1—试样浸泡后的质量,单位为克(g);
A—试样与试验液体接触部分的圆面积,单位为平方米(m2)。
取三个试样试验结果的中位数作为试验结果
厚度变化率按7.4计算。
7.9抽出物测定
7.9.1概述
如果试验液体是易挥发性液体,则从试样中抽出物质的量可用下述两种方法测定:
a)干燥试样称重法:将试样干燥处理后的质量与试验前的质量进行比较;
b)蒸发试验液体法:将试验液体蒸发干燥后,测量剩余未挥发物的质量。
以上两种方法均会产生试验误差。对于干燥试样称重法,在高温试验过程中如果有空气的存在,材
料会被氧化;对于蒸发试验液体法,在蒸发过程中会损失一些易挥发性抽出物,例如增塑剂类。本标准
两种方法都做了陈述,可根据材料的性质及试验条件进行选择。
对于易挥发性液体很难确切定义,本标准规定沸点高于110℃,蒸发量低于附录A中A、B、C、D、E
标准溶液的液体不属于易挥发性液体
抽出物的测定应在测定质量变化(7.2)、体积变化(7.3)、尺寸变化(7.4)等试验后进行
7.9.2干燥试样称重法
将浸泡后的试样在一个绝对大气压约20kPa,温度约40℃的试验箱中干燥至恒重,即每隔30min
将试样称量一次,直至连续两次称量之差小于1mg为止。
抽出物质的量以试样经浸泡并干燥后的质量与试样初始质量之差占试样初始质量的百分率表示
7.9.3蒸发试验液体法
将浸泡后的试样从试验液体中取出,并用25mL新配制的同样液体清洗试样,将清洗液体与试验
液体汇集到同一个容器中。将此容器放入一个绝对大气压约20kPa,温度约40℃的试验箱中,将液体
蒸发至恒重
同时做一空白试验,取同样的试验液体,其体积等于浸泡与洗涤试样的试验液体体积之和,并在相
同的条件下蒸发至恒重。
抽出物物质的量为浸泡试样的试验液体与洗涤试样的试验液体恒重的剩余物与空白试验液体的恒
重剩余物的质量之差占试样初始质量的百分率
8试验报告
试验报告应包括以下内容:
a)本标准编号;
b)样品描述
1)有关样品及其来源的详细说明;
2)胶料的详细说明,包括:硫化温度、硫化时间、硫化与试验间隔时间;
3)制样方法:模压或裁切;
4)试验液体描述:如是矿物油( ASTM NO.1,IRM902,IRM903,国产1、2、3号标准油除外)
8
GB/T1690—2010
还应包括密度、黏度、折光指数、苯胺点或芳香烃含量(如有必要)。
c)试验及试验方法描述
1)使用方法;
2)试样类型;
3)使用的标准实验室温度
4)试样调节的详细说明;
5)浸泡温度和时间;
6)操作程序与本标准存在的差异
d)试验结果
1)以本标准条款中规定的形式表示试验结果;
2)试样外观情况(例如脱层或裂口等);
3)试验液体外观情况(例如变色或沉淀等);
4)试验时间
e)试验日期/
GB/T1690-2010
附录
(规范性附录)
参考液体
警告:在准备或操作试验液体时应采取适当的安全措施,特别是有毒腐蚀性、易燃性液体。对于发烟液
体应在有效的通风装置下操作;腐蚀性液体应避免与皮肤或普通衣物接触;易燃液体操作时应远离热源
A.1标准模拟液体
表A.1和表A.2列出市场常用的不同组分的几种液体,它也可以作为其他液体组分的指标
表A.1不含氧化物的标准模拟液体
液体
组
成
体积分数/%
A
2,2,4-三甲基戊烷(异辛烷)
100
2,2,4-三甲基戊烷(异辛烷)
B
甲苯
30
2,2,4-三甲基戊烷(异辛烷)
50
甲苯
50
2,2,4三甲基戊烷(异辛烷)
60
D
甲苯
40
E
甲苯
100
直链烷烃(C12~C18)
80
1-甲基萘
20
注:液体B、C、D相当于不含氧化物燃油,液体F相当于民用动力柴油
表A.2含氧化物(酒精)标准模拟液体
液体
组
成
体积分数/%
2,2,4-三甲基戊烷(异辛烷)
30
甲苯
50
异丁烯
15
乙醇
2,2,4三甲基戊烷(异辛烷)
25.35°
甲苯
42.25
二异丁烯
12.68′
乙醇
4.22°
甲醇
15.00
水
0.50
10
GB/T1690-—2010
表A.2(续)
液体
组
成
体积分数/%
2,2,4三甲基戊烷(异辛烷)
45
甲苯
45
乙醇
7
甲醇
2,2,4三甲基戊烷(异辛烷)
42.5
甲苯
42.5
甲醇
它们的和占液体总体积的84.5%(体积分数)。
A.2标准油
A.2.1一般说明
A 2.1.1 ASTM No. 1
是一种“低膨胀”油,主要由溶剂萃取、化学提炼石蜡等处理的石油和其他中性油调制的混合物
A.2.1.2IRM902
是一种“中膨胀”油,主要是将天然环烷油、黏土,经过蒸馏、酸处理及溶剂的萃取制备而成
A.2.1.3IRM903
是一种“高膨胀”油,通过将天然环烷油真空精制成两种润滑油的调制混合液
A.2.1.4用途
这些标准油为典型低添加剂石油,对高添加剂油或合成油需另外准备
A.2.2要求
标准油中除可能含有微量(近似于0.1%)的抗凝剂外,不应含有其他添加剂,还应具有表A.3所示
的性能。表A.4所示也是标准油的典型性能,但是生产厂家不一定提供。
使用标准油做试验,标准油应由经认可符合标准油生产要求的指定厂家生产。若不容易获得标准
油,也可用性能完全符合A.3,长期用于橡胶测试,对于相同配方同一批次橡胶,在相同测试条件下,测
试结果与标准油相同的代用油。
表A.3标准油性能
要
求
性能
试验方法
ASTM No. 1
IRM902
IRM903
苯胺点/℃C
124士1
93±3
70±1
GB/T 262
运动黏度/(10-6m2/s)
20±1
20±1
33±1b
ISO 3104
11
GB/T1690-2010
表A.3(续)
要
求
性能
试验方法
ASTM NO I
IRM902
IRM903
闪点/℃(最低)
243
240
163
GB/T3536
密度(15℃)/(g/cm3)
0.886±0.002
0.933±0.006
0.921±0.006
GB/T1884
黏重常数
0.865±0.005
0.880±0.005
环烃含量CN/%
≥35
≥40
石蜡含量CP/%
≤50
≤45
测定温度99℃。
测定温度37.8℃。
表A.4标准油典型性能
要
求
性能
试验方法
ASTM NO. 1
IRM902
IRM903
倾点/℃
12
31
GB/T3535
折光指数(20℃)
1.4860
1.5105
1.5026
ISO 5661
芳香烃CA/%
12
14
A.3模拟工作液
A.3.1101工作液
101工作液是模拟合成柴油润滑油。由99.5%(质量分数)的癸二酸二辛酯(质量分数)和0.5%
(质量分数)吩噻嗪组成
A.3.2102工作液
102工作液组成类似于某种高压液压油。
由95%(质量分数)的 ASTM NO.1油,5%(质量分数)的碳氢混合添加剂组成的混合物。其中添
加剂中含有29.5%~33%(质量分数)的硫;1.5%~2%(质量分数)的磷;0.7%质量分数)的氮及其他
要求的添加剂。
A.3.3103工作液
103工作液是模拟航空用磷酸酯液压油(三正丁基磷酸酯)。
A.4化学试剂
使用的化学试剂应与产品实际使用试剂相同。如果没有特别规定,所用化学试剂应符
合GB/T11547规定
GB/T1690—2010
附录B
(规范性附录)
参考液体
国产1号、2号、3号标准油其主要性能应符合表B.1、表B.2的规定。
表B.1
指
标
项目
试验方法
1号油
2号油
3号油
苯胺点/℃
124±1
93±3
70±1
GB/T 262
运动黏度/(106m2/s)
20±1
20±1
33±1
GB/T 265
闪点/℃(最低)
40
24
240
160
GB/T 267
在99℃时测量;
b在37.8℃时测量
表B.
指
标
项目
试验方法
1号油
2号油
3号油
密度/(g/cm3)
15℃时
0.886±0.002
0.9335±0.0650.9213±0.0060GB/T1884
20℃时
0.882±0.002
0.9300±0.00650.9181±0.0060
折光指数
20℃时nB
1.4860±0.005
14860±0.005
1.5130±0.005
最大硫含量/%
0.3
0.3
0.3
GB/T 388
折光指数按阿贝折射计说明书进行测定
中华人民共和国
国家标准
硫化橡胶或热塑性橡胶
耐液体试验方法
GB/T1690-2010